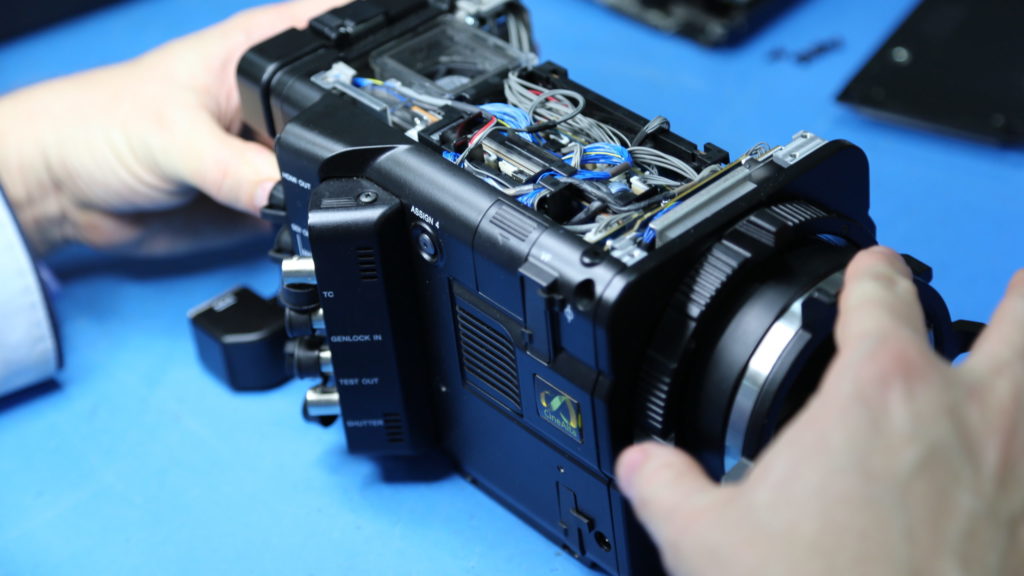
Sur ce site de 30 000 m2, 136 des 400 employés produisent et assemblent 54 produits professionnels de la ligne Sony (des caméras, des unités de contrôle, des adaptateurs). Une partie de la production pour le monde et avant tout pour l’Europe est ici prise en charge.
« L’intérêt de cette chaîne de fabrication en Europe est pluriel : les avantages sont économiques, écoresponsables, et la proximité avec les utilisateurs finaux européens nous permet d’offrir une valeur ajoutée de services. Le coût de fabrication est réduit car il faut savoir que les salaires sont plus élevés au Japon. Les frais de transport vers le bassin des clients européens sont également moins importants. Nous sommes aussi plus réactifs en termes de délais de livraison. Enfin cette localisation offre parfois la possibilité d’adapter, dans une certaine mesure, les produits aux exigences de nos clients professionnels », souligne Norbert Paquet, responsable marketing produits pour l’Europe.
Au final, chaque année, près de 14 000 produits sortent de ces lignes de production dont 6 000 produits de la gamme broadcast…
Lors de son ouverture en 1992, l’usine fabriquait des téléviseurs à tube cathodique, une activité qui s’est arrêtée en 2005. L’usine a démarré sa production de caméras avec la BVP 9000 en 1999. Une ligne de production d’exception s’est alors mise en place au fil du temps. Afin de pérenniser l’image de qualité véhiculée par la marque, les équipes de Pencoed ont développé des stations de travail spécifiques ainsi que tout un process (analyse, contrôle, prise en compte des feedbacks et suggestions des employés). Aujourd’hui, deux heures sont nécessaires pour assembler une caméra puis celle-ci est soumise à deux heures de tests avant sa mise en carton. Ces tests concernent aussi bien l’électronique que le software.
L’usine produit et assemble des P1, des Sakura et des XD Cam HD. Ainsi, depuis l’ouverture de sa ligne de production de caméras XD Cam en 2008, 9 049 unités ont été livrées et 60 204 accessoires périphériques sont sortis de ses chaînes depuis 2010. Pencoed produit aussi le software de la F65 qui est ensuite acheminé au Japon pour l’assemblage final.
Les cartes de composants électroniques que l’on retrouve, entre autres, dans les caméras sont également fabriquées sur place. Ces plaques, qui agrègent entre 100 et 2 000 composants, sont placées dans des machines capables d’opérer 10 passes par seconde. Les composants sont ensuite définitivement fixés sur la plaque via un thermo collage à 360°.
Pencoed est, par ailleurs, le seul site hors Japon qui produise des capteurs HD Tri CCD. Une machine placée dans une salle blanche dont l’atmosphère est 50 fois moins poussiéreuse que celui d’un environnement standard aligne ces capteurs au micron près. Une quarantaine de capteurs sont ainsi assemblés par jour.
Outre ses lignes de production, le Centre technologique de Pencoed héberge un incubateurde 22 start-up, une ligne de sous-traitance pour des produits intégrant des cartes de composants électroniques, un service après-vente Sony et une académie de formation y sera ouverte prochainement.
Le service après-vente de Pencoad assure la réparation de tout le portfolio des produits Sony, professionnels et grand public. Si l’objet le plus réparé est la PSP, le lieu accueille aussi tout le matériel broadcast européen dont la réparation ne peut être assurée localement. Son retour est assuré partout en Europe, dans les cinq jours qui suivent son dépôt par le client.Ce service de réparation du matériel professionnel, géré par huit techniciens et deux ingénieurs, reçoit et répare ainsi environ 70 produits professionnels par semaine (caméra, vidéoprojecteurs, pupitres…).